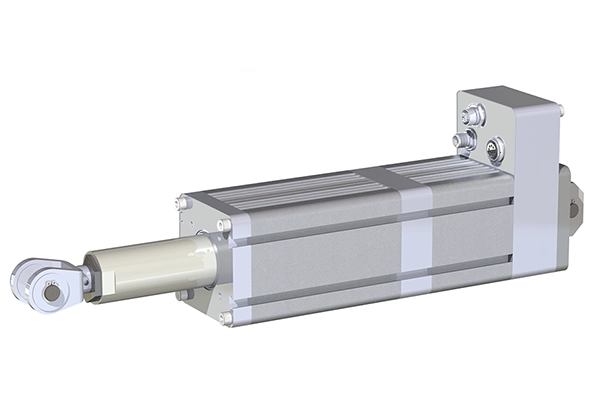
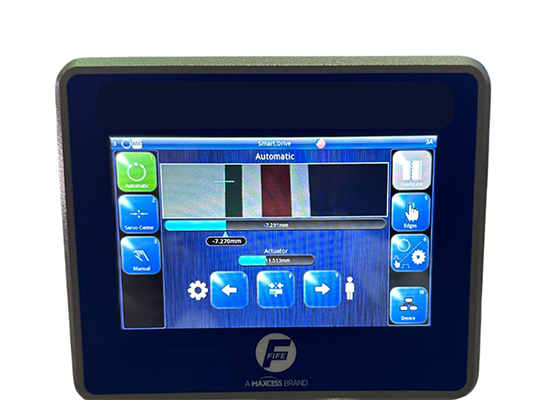
Fife SmartDrive Actuator
- Compact, all-in-one design for simple setup, easy installation, & reduced cost
- Exceptional speed & precision in correcting material position errors for consistent quality
- Stroke lengths up to 400 mm
- Zero drift, absolute position encoder and built in server
- Seamlessly integrates with all Fife DSE-Series digital sensors
- User-friendly, touchscreen operator interface
- Brushless motor for long-lasting performance with minimal upkeep
- Dual-rail power supply enables safe emergency stops without losing communication
- Flexible mounting options
- IP54-rated, suitable for various industrial environments
Fife SmartDrive Actuator Overview
The Fife SmartDrive Actuator is an advanced, all-in-one solution designed for automated edge and center guiding in converting, laminating, and printing applications. It integrates a controller, drive, and motor into a compact, easy-to-install package with superior speed, responsiveness, and accuracy. The gearless, direct-drive design ensures maximum thrust and speed throughout the entire stroke, regardless of mounting orientation. At the same time, an integrated servo center and absolute position encoder maintain precision without needing recalibration, even after power cycles. Compatible with all Fife DSE-series digital sensors, the SmartDrive Actuator delivers unmatched accuracy and simplicity in closed-loop guiding when paired with the Fife Guideline Sensor.
Applications of the Fife SmartDrive Actuator
The Fife SmartDrive Actuator is perfect for converting, laminating, and printing industries where precise material guiding and positioning are critical. Its robust design and versatile mounting options make it ideal for various industrial environments, ensuring reliable and efficient performance.
Enhance Your Automation with Fife GuideLine Sensor
Pair the SmartDrive Actuator with the Fife GuideLine Sensor for an unmatched closed-loop guiding system. This combination offers superior accuracy and simplicity, enhancing your automation processes and ensuring optimal material handling.
Thrust Force: Available in two models:
-
- 1200N (270 lbs) – Designed for applications requiring moderate force and speed.
-
- 2450N (550 lbs) – Ideal for heavy-duty applications needing higher force.
Speed:
- 1200N Model: Up to 80 mm/s (3.15 in/s) for fast and efficient operation.
- 2405N Model: Up to 60 mm/s (2.36 in/s) for applications requiring higher thrust.
Positioning Accuracy: ± 0.05 mm (50 µm) for precise material handling.
Stroke Length Options: 50, 100, 125, 150, 200, 250, 300, 400 mm to suit various application needs.
Error Correction Response: 6 Hz, providing fast and reliable adjustments to maintain material alignment.
Mounting Types: Versatile mounting options, including Clevis, Rod Eye, Trunnion, and Flange for flexible installation.
Connectivity and Communication:
- Ethernet: Modbus TCP, Maxnet for robust network integration.
- RS-485: Supports up to (3) Fife DSE Sensors and (1) Operator Interface.
- Supports Ethernet/IP, PROFINET, and EtherCAT Protocols via optional gateway for enhanced connectivity.
Power Supply Requirements:
- 1200N Model: 24V DC, 280W, 10A for efficient power usage.
- 2450N Model: 24V DC, 480W, 20A for higher performance.
Environmental Conditions: Operates efficiently between 0° C (32° F) and 60° C (140° F) with IP54-rated protection, suitable for various industrial environments.
Certifications: TUV and CE certified, ensuring compliance with international safety and quality standards.
Connectivity and Communication:
-
- Ethernet: Modbus TCP, Maxnet for robust network integration.
- RS-485: Supports up to (3) Fife DSE Sensors and (1) Operator Interface.
- Supports Ethernet/IP, PROFINET, and EtherCAT Protocols via optional gateway for enhanced connectivity.
Product Sheets
Related Products
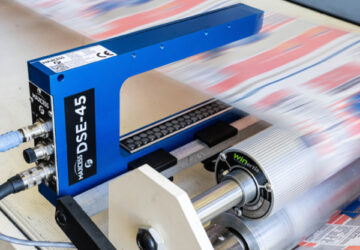
DSE-45 Wideband Ultrasonic Sensor
A high-precision wide band ultrasonic sensor that delivers reliable and accurate measurements in a variety of industrial applications.
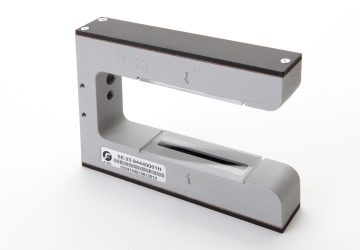
DSE-23
A high-precision ultrasonic sensor that delivers reliable and accurate measurements in a variety of industrial applications.
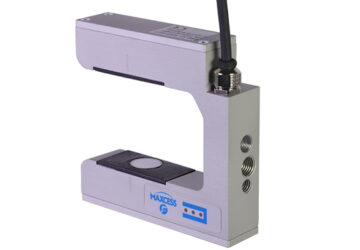
DSE-41 Digital Ultrasonic Sensor
A high-precision ultrasonic sensor that delivers reliable and accurate measurements in a variety of industrial applications.
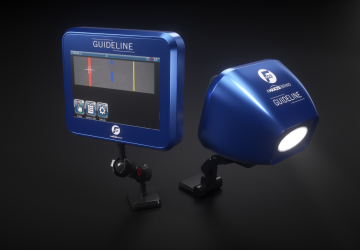
GuideLine & Guideline High Resolution (HR) Digital Line Guide Sensor Overview
Detect lines, edges of lines, graphic patterns, and more where traditional line sensors don’t work at a competitive price point. The GuideLine is suitable for the most demanding line guide applications.
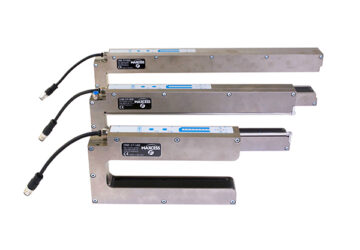
DSE-17 Digital Wideband Infrared Sensor
Most suitable for applications where opacity or density variations may occur, it can track up to 4 independent web edges simultaneously. The DSE-17 sensor eliminates the need for manual repositioning of the sensor, removing moving parts and reducing maintenance and downtime.
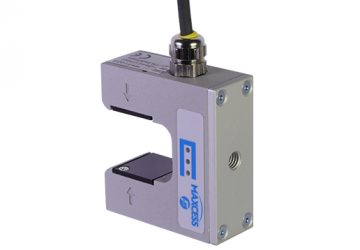
DSE-11 Digital Infrared Sensor
The DSE-11 is the smallest infrared sensor available from Fife. It’s compact, lightweight, and insensitive to ambient light, making it ideal for many applications where accurate web guiding is required and space is limited.
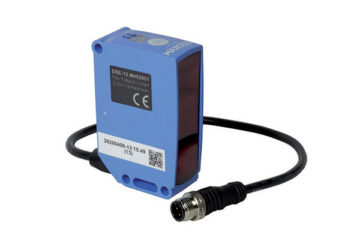
DSE-15 Reflected Light Sensor
The DSE-15 is compact and ideal for most applications where space is limited with opaque, transparent, or reflective materials.